・概要 本事例は、大型機械装置を製造されている企業殿でスケジューラを利用して、全体日程及び詳細日程を求めている例です。
製造範囲は、材料工程である鋳造から、機械加工、組立及び製品検査までの全工程に渡り、社内及び協力会社による全作業を一括して管理のうえ、製造されています 今回の導入は、既存の生産管理システムの更新に合わせ、生産計画の管理精度向上を目的として、スケジューラシステムを導入されました。 弊社は、計画管理系システム構築の立場で参画させていただき、計画管理の視点より、 - 全体日程及び詳細日程の管理方式
- 詳細日程における、最遅日程基準での計画方式
等をご紹介し、 - 業務を進めるにあたっての従来の問題点の解決策 及び 新方式での問題回避策
を、提案・調整させていただきながらシステム開発を進めさせていただきました。 以下は、開発させていただいたシステムの概要です。 ・課題 導入検討時に、客先にて課題として考えられていたことは下記の通りです。 - 受注量変動に対し、適切な対策が迅速に出来ない。
見積中の案件を含んだ負荷状況を必要の都度、Excelを用いて人手により負荷計画を実施していたため、要求に対し、タイムリーな回答が十分に出来ていなかった。
- 負荷考慮が十分でないために、実施困難な計画が出来ていた。
納期を基準とした、最遅日程での日程計画で、特定負荷を見ながら手修正していたため、注目している設備等は確保されているが、要員が足らない等で、再計画を余儀なくされる等が発生していた。
- 各計画(鋳造、加工、組立)が個別に作られ、連携は人間が調整。
各部署で決められた日程で製造するというより、それぞれの部署で計画が作成されており、生産管理部隊が、納入日基準での優先順等、全体調整を実施されていた。
- 最遅日程での管理のため、作業期間を考慮した計画になっていなかった。
納期基準での最遅日程を製造の期限日としていたため、多工程で時間がかかるものも少工程で短期に出来るものも、同じ基準で管理されていたため、急ぐものが優先されておらず、製造現場で混乱が生じていた。
- 計画者に熟練度が要求され、且つ、計画立案に時間がかかる。
計画作成には、設備、要員等の複数の資源考慮が必要です。これらの資源は、案件毎の仕様にて制限が加わるため、これらを考慮し、実施可能な資源組合せを割り出し、それぞれの資源空きを確認する作業が必要となります。これらの作業を実施するには、仕様の理解度が重要であり、熟練者で無いと正しい計画が作れない。
- 計画単位が1日の為、同一日に複数の作業を実施する等の工期短縮の計画が出来なかった。
・特徴 本システムにおける特徴は下記の通りです。(データ処理概要を 図1に示します。) - 既存システムの最新の工程マスタ情報、実績情報等を利用して、全体及び詳細日程を計画するシステムを新たに開発。
- 全体日程、詳細日程計画共に、本番計画以外に、条件を変えての複数の計画検討を可能にするWhat-If機能をシミュレーション機能で提供。
- 日程及び各種資源負荷を考慮した計画修正には、GUIインタフェースツールを提供し、容易に修正。
- 最遅日程での管理のため、作業期間を考慮した計画になっていなかった。
| 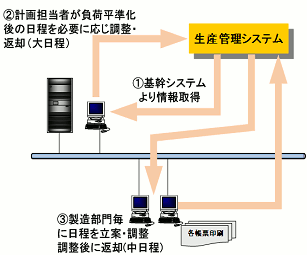 図1.処理概念図 | - 予防保全等による、設備休止を反映可能とし、設備保全計画を考慮した日程計画作成が可能。
|
・導入効果 本スケジューラ導入に伴い、下記の効果が実現されています。 - 見込み案件を含めた、負荷積みにより、早期の問題検出。
上記で述べたシミュレーション機能を活用し、種々の受注条件での負荷状況をモニターされています。
- 全体日程計画時に、負荷を考慮した、実施可能な日程計画。
組立・製品検査は、社内のみにて実施の為、全体日程計画時にも、詳細日程レベルでの負荷計算を実施し、実施可能日を算出。 又、組立開始日も、指定の範囲内で開始として、負荷制限を守るため、開始日が自動的に再計算される仕組みを折り込んでいます。 これらの処理は、同一受注内の複数号機の期日管理を含め、計算をしています。
- 全体日程における製造担当部署毎の日程算出。
組立開始日を基準として、設計、鋳造、機械加工の開始終了日程を求め、且つ、作業期間の不足する場合は、不足日数を算出し、調整を容易としています。 尚、これらで求めた日程は、マイルストーンとして、詳細日程にて利用されています。
- 詳細日程においては、全体日程のマイルストーンを基準とした、優先度を適用。
全体日程のマイルストーンを基準とすることにより、各製造部署での製造責任を明確にするとともに、急ぐものを優先して作る計画手法を適用し、予定のマイルストーン完了日を超えるもののみを部署間の調整部品とすることにより、調整作業を軽減しています。
- 機械加工においては、加工時の設備毎に材質まとめを計画作成に折り込み。
現場での切粉改修作業を簡素化するために、マイルストーン優先順を考慮しながら、材質を纏めて加工する日程計画を作成。又、昼夜の勤務人数が異なることより、夜間の材質切り替え回数が最も少なくなるようにしています。
- 計画立案のシステム化により、計画立案関係の作業時間の短縮。
システムでの計画自体は、すばやくできるようになりましたが、その時々の環境要件に応じた調整に手がかかっており、それ程効果が得られていません。
但し、資源等を考慮した計画となっており、以前に比べれば、精度向上が図られています。
- 計画単位を1時間単位とし、計画精度を向上。
従来は時間単位が1日で有ったため、2~3時間の工程でも一日を必要としていました。 このため、一日の作業といっても、実際の作業量は数時間のものなのか、一日フルに作業が有るかがいまひとつ見えていませんでした。 今回は、時間単位を1Hrにすることにより、これらの作業が時間で表現されるため、作業量が正確に見えるようになり、計画に対する信頼も向上しました。 又、時間単位にすることにより、シフト、残業も計画の中に折り込みを可能としており、実際の作業時間が見えるようになっております。
注)残業の適用方針 1)全体日程計画時 :実施時の遅れ等のリスクを残業で対応するための余裕を持たせるため、残業無で計画。 2)詳細日程計画時 :作業負荷量を考慮し、決められたマイルストーンを守る為、必要なレベルで残業を設定し、 実施可能な計画を作成。 *本Webマガジンの内容は執筆者個人の見解に基づいており、株式会社オージス総研およびさくら情報システム株式会社、株式会社宇部情報システムのいずれの見解を示すものでもありません。
|