1.概要 本事例は、機械装置を製造されている企業殿でスケジューラを利用して、受注情報から複数の受注オーダを製造型式及び納期を見ながら、製造単位としてまとめ、個々の納期を守る製造計画を立案、製造指図を発行している例です。 製造範囲は、材料のプレスによる半製品作成、部品取り付け、組立を実施されておられます。 今回のシステム範囲は、半製品製造工程の計画立案をスケジューラで構築しました。 システム導入の目的は、従来管理担当者が手作業で実施していたプレスの生産計画を
- 計画立案業務の省力化
- | 必要生産量の自動算出
| - | まとめ生産による、稼働向上
| - | 鋼材メ-カ、梱包単位を基準とした、材料引き当て計画の自動処理 |
- 生産計画の管理精度向上
- | パレット移送を考慮した工程別能力差による最早実施日程の自動計算
| - | 納期を基準とした日々の空き量を基にした、後納期品の引き込みによるまとめ生産実施による、段取り作業の軽減
| - | 人作業により従来発生していた、誤まとめによる製造数量過不足の発生防止を目的として、スケジューラシステムを選択され、導入されました。 |
弊社は、計画管理システム構築の立場で参画させていただき、従来の開発経験より、 - 手作業処理の自動化基準の設定方法
- まとめ手法の処理方式紹介
- 移送手段を考慮した際の、設備能力差の吸収方式
等を紹介し、 - 業務を進めるにあたっての従来の問題点の解決策 及び 新方式での問題回避策
を、提案・調整させていただきながらシステム開発を進めさせていただきました。 以下は、開発させていただいたシステムの概要です。 2 課題 導入検討時に、客先にて課題として考えられていたことは下記の通りです。 - 緊急品対応
- 受注以外にも、見積として緊急納入品があり、受注のみでの製造指図では不足が発生する。(緊急納入品として、製造した半製品を先に使用してしまう為に、製品製造時の半製品数が不足する事態が発生していました。)
- まとめ処理
- 従来、生産効率を上げるために、指定期間内の同一型式をまとめて生産していましたが、注文量が大幅に増えると過負荷が発生し、結果として、半製品の納期遅れが発生する場合がありました。
- メーカ別材料引き当て
- 材料は同一仕様品を複数社より購入していますが、プレスによる加工性はメーカ毎に微妙に異なります。
- この為、個々の製造時に使用する材料は同一メーカを引き当てる必要がありますが、材料在庫などを都度検索して在庫量を見ているため、各メーカの梱包毎の材料数と、製造数の引き当て調整に手間がかかっていました。
- 適切な操業時間
- 日々の受注量が変動するため、日々の操業時間を週単位で切替対応していますが、先の負荷量が見えないため操業設定が妥当か判断できませんでした。
- 実行可能な製造指図
- 材料引き当てを手作業で実施していたため、引き当てを間違える等で、
- 実施不可能な計画になっている場合がありました。
- 計画者に熟練度が要求され、且つ、計画立案に時間がかかる
- 計画作成には、材料、設備等の複数の資源考慮が必要です。
- 従来の計画立案は、半製品在庫数、材料数の確認から、製造量、材料引き当て迄を
- 全て手作業で実施していた為、計画立案に時間がかかっていました。
- 又、プレス工程はプレス作業と連動して、トリム(不要部分の切落し)、洗浄(プレス用潤滑剤の除去)が一連で作業を実施する必要があるにもかかわらず、一部の設備が他部署との共用となっているため、その調整が必要であり、熟練者で無いと正しい計画が作れない等の問題が有りました。
3 特徴 本システムにおける特徴は下記の通りです。 - まとめの自動生成及び調整
- 個々の納期を守りながら、日々の空き時間に該当する、一定期間内の後納期の受注を引込み、製造オーダとしてまとめを実施。まとめにより、段取りを削減し、生産効率を上げながら、納期を守る製造計画を自動生成しています。(図1参照)
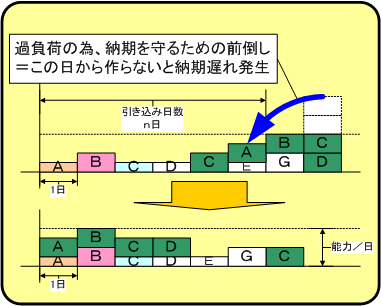 図1 まとめ方式 概念図
- 自動まとめの調整
- 製造する際の材料引当も、自動まとめの際に同時に実施しているが、共通材料となるものが多く、その調整は計画者に依存します。本システムでは、自動引当結果をユーザが関連する型式を参照しながら製造対象及び製造数の指定を容易に決定できる画面を提供し、計画熟練者で無くても、調整を容易としました。
- 搬送を考慮したスケジューリング
- 製造時の工程間搬送(パレット移動)を工程それぞれの能力を見ながら、最早の開始日基準に計画を作成可能な関係を作っております。(図2参照)
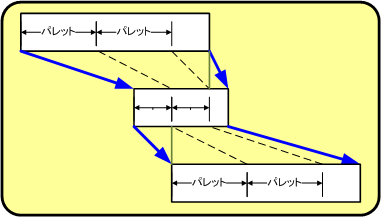 図2 搬送を考慮した異能力間工程の関係
4 導入効果 本スケジューラ導入に伴い、下記の効果が実現されています。 - 半製品の欠品防止
- 計画作成時に、緊急品を追加として登録する機能及び、安全在庫を割った際の補充生産の自動生成機能により本問題を未然に防げるようにシステム構築をしました。
- 但し、補充オーダに関しては、製造負荷量が過負荷となっているため、補充生産が十分に出来ず、製造できない分の安全在庫での管理対象部品では、依然として発生しています。
- 操業管理
- 計画立案前に、納期レベルでの、負荷量をグラフにて表示し、製造負荷の推移が分かるようになりました。この結果、ノー残業デイ等を含めた操業計画を容易に作成可能となり、長期負荷量を考慮した、計画が立案できるようになりました。
- まとめ生産
- まとめ生産実施時の引き込み量を、対象期間から、空き量での引き込みとしている為、従来のような大量注文が有った場合でも過負荷の発生が予防でき、その他小口の納期を含め、納期を守っての生産が可能となりました。
- システム化による、製造計画の作成時間短縮
- 製造計画は、
- 1)半製品在庫量、受注量の引当に基づく、製造必要量の算出
- 2)製造必要順番でのまとめを実施して、自動で素案を作成
- 3)製造指図作成画面での最終決定
の手順で実施される。 このうち、1)、2)の処理を、自動処理化した為、従来計画立案時にかかっていた時間が不要になり、計画作成時間の短縮が出来ました。
- 操作性向上による、計画作成時間の短縮
- 製造指図の作成画面では、
- ・製造対象とする、受注案件の確定
- ・生産時に利用する、メーカ毎の材料引当、引当可否チェック
- ・同一材料を複数の型式で生産する際の、個々の製番毎の生産数の調整
の機能を同時に利用可能とし、利用者の操作性を向上し計画作成時の調整を容易にするとともに、誤指示防止、計画確定の時間短縮が可能となりました。
- 共用設備の自動考慮
- 従来共用設備の利用期間を調整しながら、計画立案がなされていたが、本システムでは、製造計画のまとめを指定し、他部門の共有設備の概略使用期間を実施し、スケジューリング処理を実施することにより、他部門の共有設備利用期間が確定されるため、共用設備の利用期間調整が簡素化され、計画立案も簡単に出来るようになりました。
*本Webマガジンの内容は執筆者個人の見解に基づいており、株式会社オージス総研およびさくら情報システム株式会社、株式会社宇部情報システムのいずれの見解を示すものでもありません。 |